AI for Manufacturing Service Requests: Top 5 Use Cases
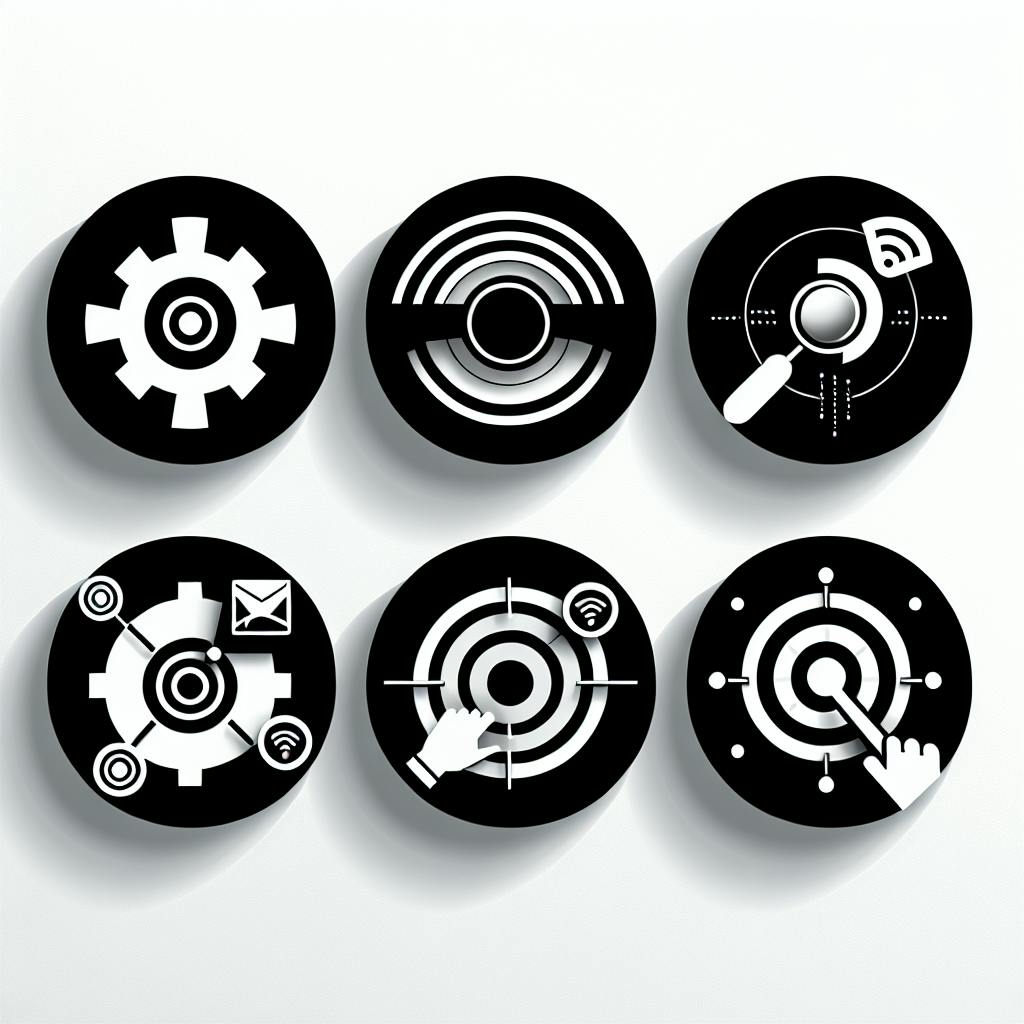
Explore the top 5 AI use cases in manufacturing service requests that enhance efficiency and customer satisfaction, from predictive maintenance to dynamic scheduling.
AI revolutionizes service request management in manufacturing by improving efficiency, reducing costs, and enhancing customer satisfaction. Here are the top 5 AI use cases:
-
Predictive Maintenance
- Identifies potential equipment failures before they occur
- Reduces equipment downtime by 30-50%
- Increases equipment lifetime by 20-40%
- Enables proactive maintenance scheduling for better customer support
-
Intelligent Chatbots
- Provide 24/7 customer support
- Quickly resolve common issues for faster resolution
- Improve information accessibility with product manuals and troubleshooting guides
- Optimize technician deployment for increased efficiency
-
Automated Remote Troubleshooting
- Detects and resolves issues before equipment failure
- Minimizes production losses and repair costs
- Enhances customer support with instant solutions
- Reduces workload for customer support agents
-
AI-powered Knowledge Management
- Centralizes knowledge sharing and automates information access
- Enables faster issue resolution and increased customer satisfaction
- Streamlines the issue resolution process for technicians
-
Dynamic Scheduling and Route Optimization
- Reduces equipment downtime by ensuring the right technician is sent at the right time
- Enhances customer support with faster and more efficient service
- Improves issue resolution efficiency by providing necessary resources to technicians
By implementing these AI solutions, manufacturers can achieve reduced equipment downtime, enhanced customer support, improved issue resolution efficiency, optimized scheduling and routing, and a competitive edge in the market.
1. Predictive Maintenance
Predictive maintenance is a crucial aspect of managing service requests in manufacturing. By using Artificial Intelligence (AI), manufacturers can identify potential equipment failures before they occur, reducing downtime and increasing overall equipment effectiveness.
Impact on Equipment Downtime
The application of AI Predictive Maintenance has a significant impact on equipment downtime. According to McKinsey, it:
Reduction in Equipment Stoppages | Increase in Equipment Lifetime |
---|---|
30 to 50% | 20 to 40% |
This means that manufacturers can minimize the likelihood of unexpected equipment failures, reduce repair times, and optimize maintenance schedules.
Enhancement of Customer Support
AI-driven predictive maintenance also enhances customer support by enabling proactive maintenance scheduling. This ensures that manufacturers can respond to customer needs more efficiently, reducing the likelihood of delays and improving overall customer satisfaction.
By adopting AI-powered predictive maintenance, manufacturers can improve efficiency, productivity, and customer satisfaction. With the ability to predict and prevent equipment failures, manufacturers can focus on delivering high-quality products and services, driving business growth and success.
2. Intelligent Chatbots for Service Requests
Intelligent chatbots are transforming the way manufacturing companies handle service requests. By using AI-powered chatbots, manufacturers can provide 24/7 customer support, automate routine tasks, and improve the overall customer experience.
Efficiency in Issue Resolution
AI-powered chatbots can quickly resolve customer issues by providing instant answers to common queries. This frees up human customer support agents to focus on more complex problems, resulting in:
- Faster issue resolution
- Reduced wait times
- Increased customer satisfaction
Improvement of Information Accessibility
Chatbots can provide customers with easy access to information on:
Information Type | Description |
---|---|
Product manuals | Detailed guides on product usage and maintenance |
Troubleshooting guides | Step-by-step solutions to common issues |
Maintenance schedules | Timely reminders for routine maintenance |
This empowers customers to resolve issues on their own, reducing the workload of customer support agents.
Optimization of Technician Deployment
By integrating chatbots with field service management systems, manufacturers can optimize technician deployment, ensuring that:
- The right technician is dispatched to the right location
- Travel times are reduced
- First-time fix rates are increased
- Overall efficiency is improved
By implementing intelligent chatbots, manufacturers can streamline their service request processes, improve customer satisfaction, and increase operational efficiency.
3. Automated Remote Troubleshooting
Automated remote troubleshooting is a powerful tool for manufacturing service requests. By using AI-powered remote diagnostics, manufacturers can quickly identify and resolve issues, reducing equipment downtime and improving customer satisfaction.
Reducing Equipment Downtime
Remote troubleshooting helps manufacturers detect potential issues before they cause equipment failure. This proactive approach:
Benefit | Description |
---|---|
Minimizes production losses | Reduces the impact of equipment failure on production |
Decreases repair costs | Lowers the cost of repairing or replacing equipment |
Improves equipment efficiency | Optimizes equipment performance and reduces waste |
Enhancing Customer Support
Automated remote troubleshooting also improves customer support by providing instant solutions to common issues. This results in:
Benefit | Description |
---|---|
Faster issue resolution | Quickly resolves customer issues, reducing wait times |
Increased customer satisfaction | Improves customer experience and loyalty |
Reduced workload for customer support agents | Frees up agents to focus on more complex issues |
By implementing automated remote troubleshooting, manufacturers can streamline their service request processes, reduce equipment downtime, and improve customer satisfaction.
4. AI-powered Knowledge Management
AI-powered knowledge management is a powerful tool for manufacturing service requests. By leveraging AI, manufacturers can centralize knowledge sharing, automate access to information, and promote a continuous learning culture.
Easy Access to Information
AI-powered knowledge management systems collect and organize vast amounts of data, making it easily accessible to those who need it. This centralized knowledge base ensures that the correct information is available at the right time to the right people.
Improved Customer Support
By utilizing AI-powered knowledge management, manufacturers can provide instant solutions to common issues, improving customer satisfaction and loyalty. This results in:
Benefit | Description |
---|---|
Faster issue resolution | Quickly resolves customer issues, reducing wait times |
Increased customer satisfaction | Improves customer experience and loyalty |
Efficient Issue Resolution
AI-powered knowledge management streamlines the issue resolution process, enabling technicians to quickly access relevant information and resolve issues more efficiently. This reduces the time spent on resolving issues, freeing up technicians to focus on more complex problems.
By implementing AI-powered knowledge management, manufacturers can improve information accessibility, enhance customer support, and increase efficiency in issue resolution, ultimately leading to improved customer satisfaction and reduced costs.
5. Dynamic Scheduling and Route Optimization
Dynamic scheduling and route optimization are essential components of AI-powered manufacturing service requests. By leveraging AI capabilities, manufacturers can optimize their scheduling and routing processes, leading to improved efficiency, reduced costs, and enhanced customer satisfaction.
Reducing Equipment Downtime
AI-powered dynamic scheduling and route optimization can significantly reduce equipment downtime by ensuring that the right technician is sent to the right job at the right time. This minimizes delays and ensures that issues are resolved quickly, reducing the likelihood of extended downtime.
Benefit | Description |
---|---|
Minimizes production losses | Reduces the impact of equipment failure on production |
Decreases repair costs | Lowers the cost of repairing or replacing equipment |
Improves equipment efficiency | Optimizes equipment performance and reduces waste |
Enhancing Customer Support
By optimizing routes and schedules, manufacturers can provide faster and more efficient service to their customers. This leads to increased customer satisfaction and loyalty, as customers receive prompt and reliable support.
Efficiency in Issue Resolution
AI-powered dynamic scheduling and route optimization enable technicians to resolve issues more efficiently by providing them with the necessary information and resources to complete jobs quickly and effectively. This reduces the time spent on resolving issues, freeing up technicians to focus on more complex problems.
By implementing dynamic scheduling and route optimization, manufacturers can improve equipment uptime, enhance customer support, and increase efficiency in issue resolution, ultimately leading to improved customer satisfaction and reduced costs.
Conclusion
In this article, we explored the top 5 AI use cases for manufacturing service requests, highlighting their benefits and applications in improving efficiency, reducing costs, and enhancing customer satisfaction.
By implementing these AI solutions, manufacturers can achieve significant advantages, including:
Advantage | Description |
---|---|
Reduced equipment downtime | Minimize production losses and repair costs |
Enhanced customer support | Improve customer experience and loyalty |
Improved issue resolution efficiency | Resolve issues quickly and effectively |
Optimized scheduling and routing | Reduce travel times and increase first-time fix rates |
Competitive edge | Stay ahead of the competition in the market |
As the manufacturing industry continues to evolve, embracing AI-powered solutions is crucial for manufacturers to stay competitive and achieve success.
We encourage manufacturers to consider implementing these AI solutions to improve their service request management. With AI, the possibilities are endless, and the benefits are undeniable.
FAQs
How does AI help in manufacturing?
AI helps manufacturers in several ways:
Area of Improvement | Description |
---|---|
Product Quality | AI analyzes data to detect anomalies and predict maintenance needs, ensuring consistent product quality and minimizing waste. |
Efficiency | AI optimizes processes, reducing downtime and improving overall efficiency. |
Customer Satisfaction | AI enables manufacturers to respond quickly to customer needs, improving customer satisfaction and loyalty. |
By leveraging AI solutions, manufacturers can improve their overall efficiency, reduce costs, and enhance customer satisfaction.
Ready to Transform Your Phone System?
See how Dialzara's AI receptionist can help your business never miss another call.